Exploring MIG 250: An Essential Technological Approach for Electricity Suppliers
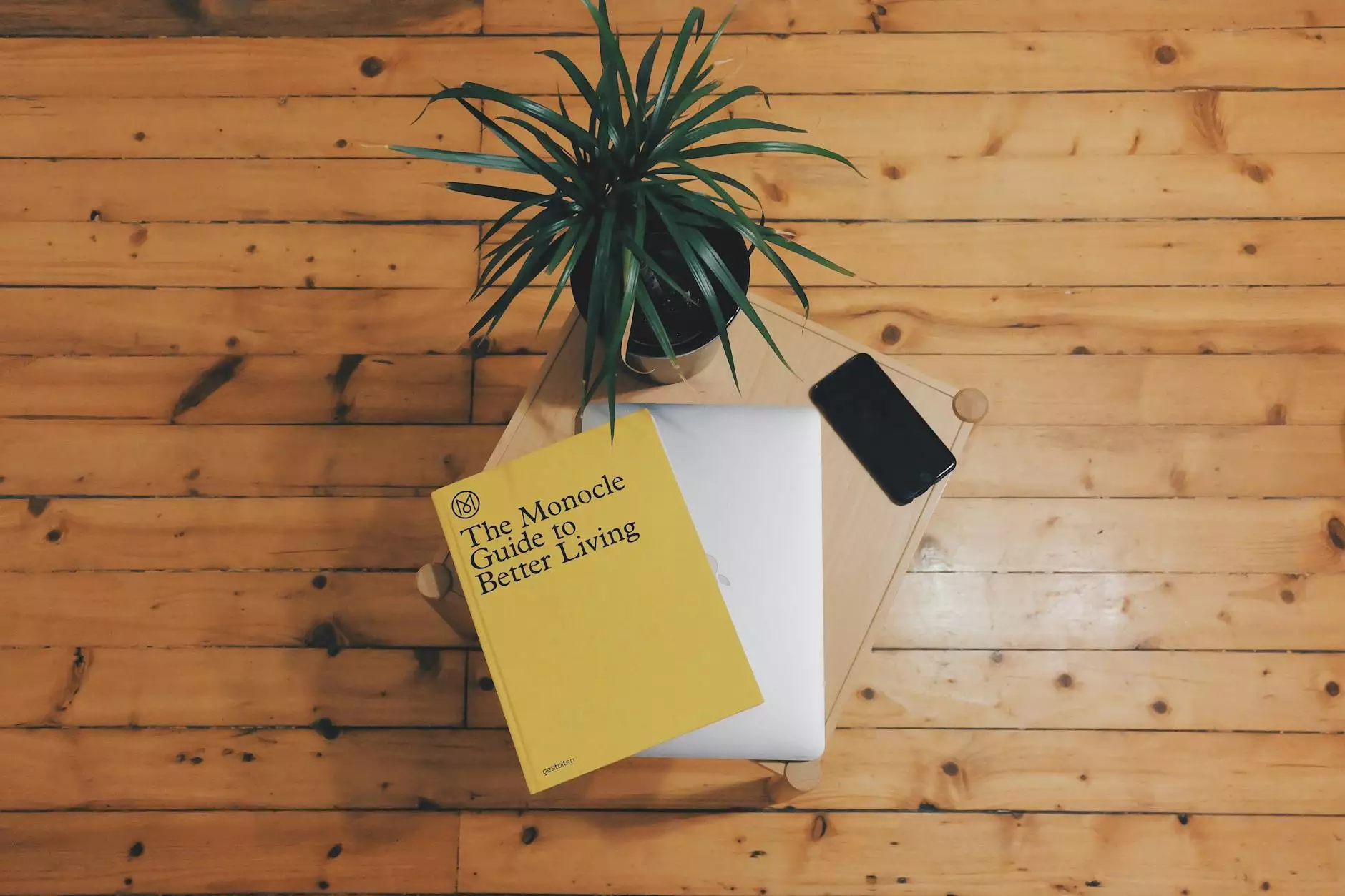
The world of business is ever-evolving, especially within the Electricity Suppliers industry. Staying ahead requires a keen understanding of the technologies that drive efficiency and craftsmanship. Among these technologies, the MIG 250 stands out, particularly in applications that intertwine with electrical services. This article delves deep into what MIG 250 is, how it impacts the electricity supply sector, and why it should matter to your business.
What is MIG 250?
MIG stands for Metal Inert Gas welding, a process that uses a continuous wire feed to create a weld. The MIG 250 refers to specific MIG welding machines that are designed to operate at 250 amps, allowing for significant welding versatility and capability. This technology is extensively used in various structural and fabrication applications, making it invaluable for suppliers in the electricity sector who might need structural enhancements or specialized project requirements.
The Importance of MIG in the Electricity Supply Sector
In the context of electricity supply, MIG technology, particularly the MIG 250, brings about several critical benefits:
- Enhanced Efficiency: The MIG 250 allows for faster welding speeds and a more efficient weld pool, which leads to quicker project completion times.
- Versatility: Able to weld various materials including aluminum, stainless steel, and mild steel, the MIG 250 is adaptable to different project requirements.
- Better Aesthetics: The smooth finish provided by MIG welding presents an advantage when visual appearance is essential, making it suitable for display structures in the electricity supply sector.
- Reduced Post-Weld Cleaning: The cleaner welds produced by the MIG 250 often require less cleaning and finishing work.
Applications of MIG 250 in the Electricity Sector
The applications for MIG 250 welders are vast within the electricity supply industry. Here are a few notable uses:
1. Fabrication of Electrical Components
Electrical components such as conduits, panels, and supports often require robust fabrication. Utilizing the MIG 250 ensures that these components are constructed with precision and strength, meeting industry standards.
2. Repairing and Maintaining Structures
Electricity suppliers often face the need to repair existing infrastructures such as pylons and transmission systems. The integration of MIG 250 welding technology enables swift and effective repairs, minimizing downtime.
3. Custom Equipment Manufacturing
In many cases, unique projects require bespoke equipment. The adaptability of the MIG 250 makes it an excellent choice for custom fabrications tailored to specific customer needs.
Advantages of Using MIG 250 Over Other Welding Techniques
When evaluating various welding techniques available for electricity suppliers, the MIG 250 offers several advantages:
- Speed: MIG welding is known for its fast operation which helps projects stay within their timelines.
- Ease of Use: The learning curve for MIG welding is relatively low, making it accessible for team members needing quick training.
- Less Waste: The continuous wire feed system of the MIG 250 leads to less wasted material compared to other welding methods.
How to Choose the Right MIG 250 Welder
Choosing the right MIG 250 welder for your manufacturing or repair shop can significantly impact your operations. Here are some key factors to consider:
1. Power Supply
Most MIG 250 welders require a dedicated power supply. Ensure the voltage requirements match your local supply to avoid operational issues.
2. Portability
Depending on your business needs, consider whether a portable MIG 250 welder is more advantageous, especially for on-site repairs and projects.
3. Duty Cycle
The duty cycle represents how long the machine can operate before needing to cool down. For heavy use, opt for a welder with a higher duty cycle.
Maintenance Tips for Your MIG 250 Welder
Ensuring that your MIG 250 welder is well-maintained can prolong its lifespan and maintain high-quality welds. Here are some practical maintenance tips:
- Regular Cleaning: Clear away spatter and debris regularly to maintain performance.
- Check Connections: Ensure all cables and connections are tight and free from wear.
- Inspect Cooling Fans: Make sure the cooling fans are not blocked, as adequate airflow is essential for operating temperatures.
The Future of Welding in the Electricity Supply Industry
As the industry evolves, the role of technologies like MIG 250 will only expand. Innovations in welding technology promise improvements in efficiency and quality that can transform how electricity suppliers operate. New materials and welding techniques will continue to emerge, enabling businesses to tackle more complex challenges.
Conclusion
Understanding the capabilities and advantages of MIG 250 technology is crucial for Electricity Suppliers aiming to stay competitive in a challenging market. From its efficiency and ease of use to its substantial versatility, the MIG 250 stands as a pillar of modern welding practices. Investing in this technology not only enhances the quality of workmanship but also positions your business for future growth.
As you navigate the challenges and opportunities within the electricity supply industry, consider how MIG 250 welding can play a vital role in your operational strategy. Embracing this technology can significantly contribute to both immediate project success and long-term viability in a competitive landscape.